If you’ve spent any time researching or reading about knives, whether pocket knives, EDC knives, survival knives, or kitchen knives, you would inevitably have seen some mention of the steel used to craft the blade. As with any slightly technical element in the outdoor space, there are, of course, “steel experts” in almost any conversation where two or more weekend warriors camp out together!
You probably shouldn’t take too much advice from them, but if you’re the average guy, you also don’t need a profoundly technical discussion by a steel maven that’ll end up confusing you more than helping you make an intelligent purchase decision.
To bridge that gap, here’s a quick guide to help demystify some of the elements and considerations involved in creating and ultimately selecting steel for a knife blade.
Why Is Blade Steel Important?
To understand why your choice of blade steel matters, you have to understand some of the properties of the different types of knife blade steel and how it impacts the function and performance of your knife.
Blade Steel Properties:
- Hardness – is an indication of a material’s resistance to an indentation that is not temporary (it persists even after the load conditions are removed, as opposed to strength which is an indication of its performance only when the load is applied) and is measured using the Rockwell C Scale (more on the Rockwell scale below). Thus a blade steel’s hardness is an important factor because the harder a blade steel is, the better it will resist edge wear and edge rolling, which are two of the major factors of edge degradation. Thus, it is helpful to know that its Carbon content mostly determines a blade steel’s hardness.
- Strength – is the ability to take a load without permanently deforming. Therefore, in blade steels, strength is directly related to hardness, and thus, the harder blade steel is, the stronger is it is. Consequently, a higher degree of strength means that a knife blade’s edge can be made thinner because it will be less prone to rolling. But, it should also be noted that, as a general rule, strength and toughness are opposed. Thus, raising the hardness of steel usually lowers its toughness and vice versa. Therefore, decreasing the grain size is the only means by which both strength and toughness can be increased simultaneously. Consequently, it should be noted that its Carbon content mostly determines a blade steel’s strength.
- Toughness – is the ability to withstand an impact without damage and, in reference to blade steels, that means resistance to cracking and/or chipping. Thus, a given blade steel’s toughness determines how well it will hand shock and the extent to which it may undergo deformity but still not break. Thus, a blade steel’s toughness is also an important factor because the tougher a blade steel is, the better it will resist microchipping, which is another major cause of edge degradation. Therefore, toughness is an important property to consider when choosing a heavy-duty chopping knife such as a camp knife or a machete. The steel’s Manganese content generally determines it. However, some of the other elements also increase toughness (aka tensile strength) and/or create a fine grain structure.
- Wear Resistance – is, of course, the ability of blade steel to withstand abrasion. Generally, the amount, type, and distribution of carbides within the steel determine its wear resistance. Therefore, wear resistance is directly related to a blade steel’s edge holding ability which, in turn, is related to its Carbon, Chromium, Molybdenum, and/or Vanadium content.
- Edge Holding Ability – is, of course, the ability of blade steel to hold an edge but, while the two are related, many people make the mistake of confusing wear resistance with edge holding ability. However, edge holding ability is actually a function of strength, toughness, and wear resistance. Thus, it is a job-specific term because different purposes require blade steels to have different properties. For instance, when using a camp or survival knife to chop and/or baton saplings, it is essential to have tough steel that won’t break but, when removing the hide from a game animal, it is crucial to have hard steel that won’t lose its edge. Yet, when working in the kitchen, corrosion can quickly dull an edge, and thus, corrosion resistance becomes a critical factor when choosing a kitchen knife. Therefore, the edge holding ability of the given blade steel is relative to the user’s intended purpose.
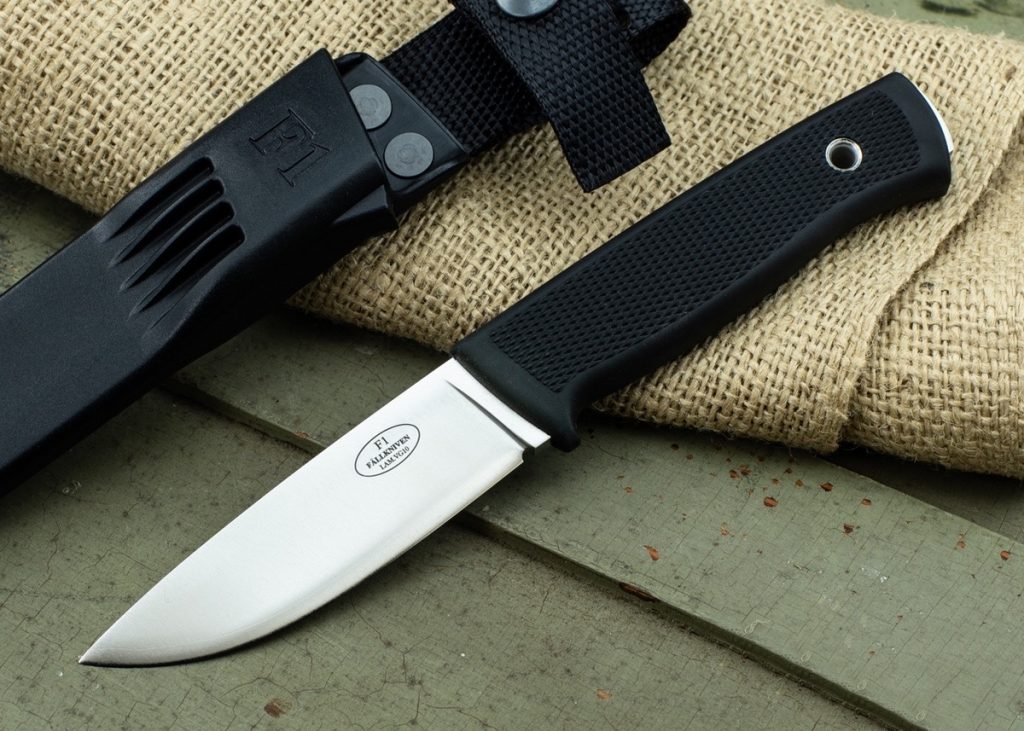
The Definition of Steel
Steel is defined as iron, containing at least 0.02% and no more than 2.10% Carbon. To be classified as high carbon steel, it must have at least 0.50% but, I should note that iron can only absorb a maximum of 0.80+% Carbon, and thus, any content over 0.80+% serves to create carbides.
Stainless vs. Non-Stainless Steels
According to the SAE steel grading system, blade steel must contain at least 10.5% Chromium to qualify as stainless steel but, the commonly accepted ratio is 12%. Therefore, stainless steels are far more corrosion resistant and hold an edge better than non-stainless blade steel but, they are more challenging to sharpen, and they do not take as fine an edge as a high carbon Plain Tool Steel. Whereas non-stainless, high carbon blade steels are much tougher, are easier to sharpen, and can take a finer edge than stainless steels, they do not hold it as well.
Steel Alloying Elements
- Carbon – is not an alloying element since it is present in plain carbon steel. Nonetheless, increasing carbon increases hardness.
- Chromium – improves hardenability, wear-resistance and, corrosion resistance. It is a major element in Martensitic stainless steels, most commonly used for sports cutlery applications.
- Nickel – improves hardenability, toughness and, corrosion resistance. Nickel is a major element in Austenitic stainless steel that is sometimes used for diving knives.
- Molybdenum – improves hardenability, tensile strength, and corrosion resistance, particularly pitting.
- Vanadium – improves hardenability and promotes a fine grain structure.
- Manganese – Increases hardenability and toughness in non-stainless steels and helps produce a fine grain structure in stainless steels by reducing the size of the Carbides.
- Tungsten – Helps to produce a fine, dense grain structure.
- Cobalt – Increases strength and hardness by producing a fine grain structure and permits quenching at higher temperatures. Also, it intensifies the individual effects of other elements in more complex steels.
- Phosphorus – Improves strength, machinability, and hardness.
- Silicon – Increases tensile strength in steel.
That’s all fine, and well, I can hear you say, but how am I supposed to remember that? Chances are you won’t, which brings me to the Rockwell Hardness Scale.
Rockwell Hardness Scale
The Rockwell scale is a hardness scale based upon the indentation hardness of a material. The Rockwell test determines the hardness of a material by measuring the depth to which an indenter penetrates under a given load, compared to the penetration made by a preload. Penetrators are made from different materials, and penetrators with different dimensions are used to test different materials. Therefor, different scales are also used, such as HRA, HRB, and HRC.
So, the Rockwell Hardness C Scale is used to test blade steels, and all blade steel Rockwell Hardness designations are expressed as a number followed by the capital letter C. Almost all blade steels have a Rockwell Hardness between 50 HRC and 65 HRC with 50 to 53 designating relatively soft blade steels, 54 to 57 designating medium hard blade steels, and 58 to 62 designating hard blade steels.
Here comes the part that you have to remember!
As a general rule, the harder blade steel, the better it will hold an edge but, the more difficult it will be to sharpen and the more prone it will be to break under stress. On the other hand, the softer blade steel is, the less prone it is to hold an edge but, the easier it will be to sharpen and the less prone it will be to break under stress.
This distinction is important when choosing blade steel for any given purpose because heavy-duty knives, like survival knives generally need to be impact resistant and easy to sharpen whereas, hunting knives generally need to be designed to hold an edge exceptionally well even if they are difficult to sharpen and, pocket, folding, and utility knives are best with blades that are in between hard and soft.
If nothing else, pay attention to the Rockwell Hardness of the blade on any knife you choose for any given purpose to help you choose the right blade steel for your intended purpose.